はじめに: 本記事の概要と想定読者
本記事では、製造業の現場で必ず起こる、突然の異常(製品特性、設備など)が起こったときの実践的で具体的な対応方法を4つのステップで解説します。配属4ヶ月で前任も上司も異動し、過去の知見を活用しづらい環境の中、2年で50件以上のトラブルを解決に導いた自称トラブル解決のプロが導き出したノウハウを皆さんに共有したいと思い、記事に起こしました。この記事を読んでステップを実践すれば、異常が起こったときも迅速に解決まで導き、歩留まりの低下や工程のストップによる損失を回避する助けになるはずです。
本記事の想定読者:
- トラブルに悩む製造業のエンジニア
- 生産ラインを担当するエンジニア
- 工場の管理職
- 製造業のトラブルに興味のある方
製造現場の定常運転が難しい理由
そもそも、なぜ突然の特性異常が起こるのでしょうか?多くは以下の項目に原因があると考えられます。
- 設備の経年変化
- オペレーターの習熟度の差
- 原材料の差
- ノウハウの逸失
- 外乱
設備の経年変化による影響
設備の経年変化は定常運転を妨げ、なおかつ検知が非常にむずかしいため厄介です。設備の状態を一定に保つため、多くの企業で設備の定期修繕を行っています。しかし、一度の修繕で、配管の内壁や装置内まですべてリフレッシュすることは現実的ではないことがほとんどです。
また、現状の運転条件が、リフレッシュされていない装置を使うことに最適化されていることもほとんどであり、リフレッシュすることで装置状態が大きく変化し、定常運転が困難になる問題もあります。私自身も、最近、10年間使い続けていた真空装置を開放し、リフレッシュした結果、一から運転条件を組み直さなければいけない自体になりました。
通常使用による装置状態の変化は緩やかに進んでいく場合が多いため、突発的な異常の原因にならない場合がほとんどでしょう。しかし、本当に経年変化に原因があるときは検知が困難であるとも言えます。
オペレーターの習熟度の違い
オペレーターによる習熟度の差も異常の原因になり得ます。多くの製造ラインでは、オペレーターのスキル表や認定制度を使って、技量の管理を行っています。しかし、あくまで一定レベル以上の技能があることを示すだけで、ベテランと新人の区別をつけることは出来ません。「誰がやっても、同じ作業と結果になる」ことを目指すためのスキル表ではあるものの、完璧であることはないと言えるでしょう。
これまで意識されてこなかった作業や作業方法に異常のタネがあるケースもあります。私個人の身近な例を挙げると、モノを右から取るか、左から取るかで結果が変わる、ということもありました。
ある工程でたまに微量ゴミの付着により収率が低下することがありました。調べたところ、どうやらAさんが作業をするときに起こりやすいことが分かりました。Aさんはベテランで、スキルも申し分ないことは自他ともに認められています。念の為Aさんの作業を見ていると、Aさんだけ半製品を左手側に置き、右に向かって移動させていることに気づきました。どうやら左から右に移動させる間に、パーティクルが付着することがあり、収率を低下させていることが分かりました。以降は全員統一して右手側に半製品を置いて作業することで、収率は安定しました。
上記の事例は当然スキル表にも反映しましたが、オペレーターは絶対に均質ではありません。そのため、オペレーターの習熟度の差は見逃せないポイントになります。
原材料のロット差
原材料の差も見逃せないポイントです。サプライヤーと取り決めたスペックに依って厳格に管理されているものの、異常の起点を追っていくと、原料のロットが切り替わったタイミングで起こっていたというケースも多いです。私自身も、まとめて購入した原料の中に、規格に十分収まっているにも関わらず、製品に使用すると必ず不良が発生する原料が混ざっていることがありました。
規格内だけど不良品、というケースもあるため、原材料の切り替わりは注意すべきポイントです。
ノウハウの逸失問題
ノウハウの逸失はここ数年、どこのメーカーであっても喫緊の課題になっているのではないかと推察しています。ちょうどバブル期入社のベテランオペレーターが引退するタイミングであり、就職氷河期の影響でノウハウの継承が出来ていない企業も多いと思われます。マニュアル化はされていないけど、実はちょっとした工夫があり、それが特性の微調整に効いているケースもあったりします。
ベテランオペレーターの引退だけでなくても、異動や退職で突然担当エンジニアがいなくなることもあります。私自身も、前任や前前任が2〜3年周期で退職や異動でいなくなり、引き継ぎのほとんど出来ない状態で生産ラインを任される事になってしまいました。上司も配属から4ヶ月で急に異動になり、ノウハウが逸失した状態で上司の仕事も一部担当する事態となりました。
私のようなケースは稀ではあると思いますが、引退や退職、異動によるノウハウの逸失がないようチーム内で知識を共有する取り組みは今後必須です。
外乱・環境の影響
外乱や環境による影響も実は重要です。空調管理された室内で生産している場合であっても、夏は湿度が高く、冬場は乾燥していたりすることもあります。例えば半製品の表面が乾く速さが変わり、それによって出来栄えに影響が出る場合もあります。
異常が発生したときは環境や何処かで工事など外乱がなかったか?は気にすべきポイントになります。
異常発生時の実践的な4ステップ
異常の原因になりうる物事は様々ありますが、原因究明の方法は基本的には同じです。以下の4ステップを実行することで、多くのトラブルは解決に導くことが出来ます。
- 現場・現物・事実を確認する
- 変化点を洗い出す
- 物差しに問題がないか確かめる
- 変化点を起点とした異常発生の仮説を立てる
ステップ1: 現場・現物・事実を確認
まずは基本ですが、異常が発生している現場と異常の事実、そして現物と正常品の比較です。どういった異常なのか、正確な事実を掴み、異常が発生している現場特定したうえでよく観察することが解決のファーストステップになります。これを怠ると、後々痛い目に遭います。
直近の私の例だと、設備に普段つかない傷のようなものが付くようになりました。僅かな傷ではあったものの、一旦生産を止めて設備の動きの確認を実施しました。すると、普段見えないところで、半製品の運搬キャリアと設備が干渉していることが分かりました。
常に現場を見ていることで、異常に気づき、トラブルを未然に防ぐことにも繋がります。まずは現場・現物・事実を注視することから始めてください。
ステップ2: 変化点を洗い出す
次は、変化点を洗い出す作業です。私の場合は、データを時系列で並べたあと、グラフ上に点線で変更した内容を差し込んでいくような形でまとめます。異常は何かしらの変化を起点にして起こるため、異常の事実と発生箇所が分かったら、変化点を洗い出す作業を実施することを推奨します。
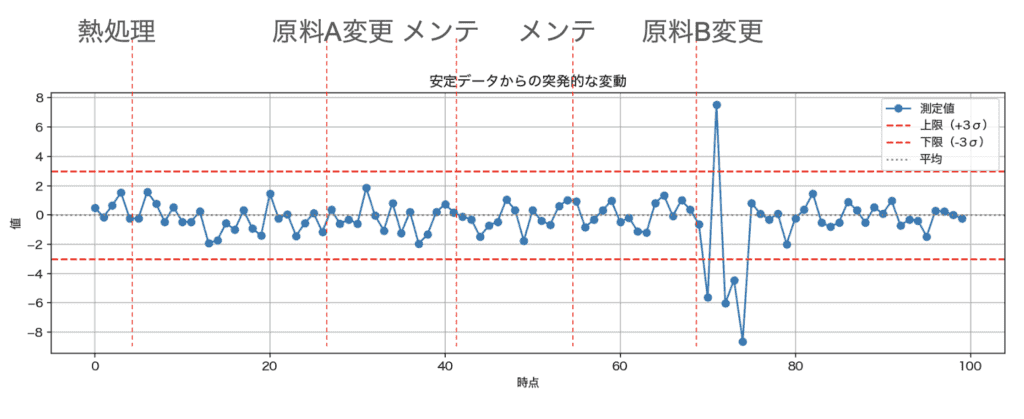
ステップ3: 検査機器の信頼性の確認
モノサシとして使っている、検査機器に問題がないかを確認することも重要です。検査機器が誤っていれば、不良に対するすべての対策は無駄に終わります。検査機器の評価は年次で行うMSAの実施などがあると思いますが、簡易的には特性値が分かっているマスターサンプルを使った評価も有効です。
MSAについては、過去の記事で実施方法も含め詳しく解説しています。ぜひご一読ください。
ステップ4:変化点を基に異常発生の仮説を構築
事実と現物、現場を確認し異常とその発生点を確認し、変化点を調べ上げ、検査機器に問題ないことを確認したら、最後は変化点と異常をつなげる仮説を立てます。これがエンジニアとしての本質的な仕事です。立てた仮説を元に、原因を立証し、対策を立てます。簡単に書いていますが、ここが一番の勝負どころです。
まとめ: 地道に事実を積み重ねれば対策は必ず見つかる
以上、製造現場で起こる異常の原因の代表例と、異常が発生したときの対処に向けた4ステップを解説しました。
- 現場・現物・事実を確認する
- 変化点を洗い出す
- 物差しに問題がないか確かめる
- 変化点を起点とした異常発生の仮説を立てる
とにかく上記4点を愚直に実行することが解決の糸口になります。
コメント